Hydrostatic Test required by API SPEC 5L 2018
Test pressures for each size of SMLs pipe and for welded pipe with D≤457mm( 18. 000 in. shall be held for not less than 5 seconds.
Test pressures for welded pipe with D> 457mm( 18. 000 in.)shall be held for not less than 10 seconds.
For threaded-and-coupled pipe, the test shall be applied with the couplings made up power-tight if agreed, except that pipe with D> 323. 9mm( 12. 375 in. ) may be tested in the plain-end condition.
For threaded pipe furnished with couplings made up handling-tight, the hydrostatic test shall be made on the pipe in the plain-end, threads-only, or coupled condition unless a specific condition is specified in the purchase order.
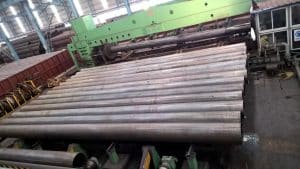
In order to ensure that each length of pipe is tested to the required test pressure, each tester,except those on which only continuous welded pipe is tested, shall be equipped with a recording gauge that can record the test pressure and the test duration for each length of pipe, or shall be equipped with some positive and automatic or interlocking device to prevent pipe from being classified as tested until the test requirements (pressure and duration have been met. Such records or charts shall be available for examination at the manufacturer’s facility by the purchaser’s inspector, if applicable. The test pressure-measuring device shall be calibrated by means of a dead-weight tester, or equivalent, no more than four months prior to each use. At the option of the manufacturer, test pressures that are higher than required may be used.
Test Pressure: How to calculate the hydrostatic test pressure?
ASME 31.3 Piping Materials – Allowable Pressure Calculator
The pipe shall withstand the hydrostatic test without leakage through the weld seam or the pipe body. The hydrostatic test pressure, P, expressed in megapascals (pounds per square inch), for plain-end pipe shall be determined using Equation P=2St/D, with the results rounded to the nearest 0,1 MPa (10 psi):
where
‘S’ is the hoop stress, expressed in megapascals (pounds per square inch), equal to a percentage of the specified minimum yield strength of the pipe, as given in Table below;
‘t’ is the specified wall thickness, expressed in millimeters (inches);
‘D’ is the specified outside diameter, expressed in millimeters (inches).
NOTE: The specified test pressure represents the gauge pressure value below which the pressure is not permitted to fall during the specified test duration.
Table 26-Percentage of Specified Minimum Yield Strength for Determination of S | |||
---|---|---|---|
Pipe Grade | Specified Outside Diameter D mm(in.) | Percentage of Specified Minimum Yield Strength for Determination of .S |
|
Standard Test Pressure | Alternative Test Pressure | ||
L175 or A25 | ≤141.3(5.563) | 60a | 75a |
L175P or A25P | ≤141.3(5.563) | 60a | 75a |
L210 or A | Any | 60a | 75a |
L245 or B | Any | 60a | 75a |
L290 or X42 to L830 or X120 | ≤141.3(5.563) | 60b | 75° |
>141.3(5.563)to 219.1(8.625) | 75b | 75° | |
>219.1(8.625) to <508(20.000) | 85b | 85 | |
≥508(20.000) | 90b | 90° | |
a For D88.9 mm(3.500 in.), it is notnecessary that the test pressure exceed 17.0 MPa(2470 psi); for D >88.9 mm(3.500 in.), it is not necessary that the test pressure exceed 19.0 MPa (2760 psi). b It is not necessary that the test pressure exceed 20.5 MPa (2970 psi). c For D ≤406.4 mm(16.000in.), it is not necessary that the test pressure exceed 50.0 MPa (7260 psi); for D > 406.4mm(16.000 in.), it is not necessary that the test pressure exceed 25.0 MPa (3630 psi). |
*Apply to API 5L line pipes
Hydrostatic Test operation procedure
Pipeline Hydrostatic Test is an important part of ensuring the normal operation and safety of pipeline systems. Before carrying out the hydraulic pressure test, we need to carry out a comprehensive inspection and preparation of the piping system to ensure the accuracy and reliability of the test results. The following will detail the steps and precautions for the pipeline hydrostatic inspection test.
First of all, before carrying out pipeline water pressure testing, we need to prepare some necessary tools and equipment, including pressure gauges, pumps, valves, water pipes and so on. The selection of these equipments should be made according to the specific conditions and requirements of the piping system to ensure the accuracy and reliability of the test.
Next, we need to conduct a comprehensive inspection of the piping system, including the sealing of the pipes, whether the connection parts are tight and whether there are any leakage problems. During the inspection, special attention should be paid to the various connection parts of the piping system, such as flanges, threads, welds, etc., to ensure that they can withstand the test pressure without leakage.
After making sure that the piping system is well sealed, we can start the water pressure test. First, you need to close all the valves of the piping system and connect the water pump to the piping system. Then, gradually turn on the pump and inject water into the piping system while observing the change in the pressure gauge reading. When the reading of the pressure gauge reaches the test pressure required by the design, turn off the pump and observe whether the reading of the pressure gauge remains stable.
During the test, special attention needs to be paid to the following points: first, make sure that the piping system has been filled with water and air has been eliminated to avoid errors in the test results; second, calibrate and verify the pressure gauge to ensure its accuracy and reliability; finally, make sure that no one enters the test area during the test to ensure the safety of the test.
If the test results show that there are leaks or other problems in the piping system, they need to be treated and repaired in time. After repairing, hydrotesting should be carried out again to ensure that the sealing and pressure-bearing capacity of the piping system meets the design requirements.
In addition to the above mentioned precautions, the following points need to be noted: firstly, the piping system should be cleaned and sterilized before the hydraulic test to ensure that there are no impurities and bacteria inside the piping; secondly, the piping system should be regularly inspected and maintained during the testing process to ensure its normal operation and safety; lastly, after the test is finished, the piping system should be drained and dried in order to avoid corrosion and damage inside the pipeline.
In short, pipeline Hydrostatic Test is to ensure the normal operation of the pipeline system and an important part of the safety. Before the test, the piping system needs to be comprehensively inspected and prepared, and pay attention to the safety matters in the testing process. If problems are found in the piping system, they should be handled and repaired in time to ensure its normal operation and safety.
LONGMA is a proffesional API 5L LSAW steel pipes/line pipes manufacturer since 2003, all our API 5L B LSAW steel pipes, API 5L X42 line pipe, API5L X52 pipe, API 5L GR X60 LSAW pipe, API 5L PSL1 & API 5L PSL2 steel pipes will take 100% hydrostatic test.
Contact us by info@ilongma.com to get more information.