As global energy demand continues to rise, the oil and gas industry faces unprecedented challenges and opportunities. A critical component of infrastructure within this sector is the steel pipe, where the quality and performance directly impact the safety and efficiency of oil and gas transportation. ASTM A671 steel pipes, with their exceptional corrosion resistance, strength, and reliability, have become an indispensable material in the oil and gas industry. Whether used in extreme environments or subjected to the rigors of long-distance transportation, ASTM A671 steel pipes ensure the stable operation of pipelines. This article will explore the key role of ASTM A671 steel pipes in the oil and gas industry, and why they stand out in an increasingly competitive market, becoming an integral part of industry standards!
ASTM A671 Steel Pipe Overview
ASTM A671 is a standard specification for electric-fusion-welded steel pipes with added filler metal, designed for high-pressure service at atmospheric and lower temperatures. These pipes are fabricated from pressure vessel-quality plates of various analyses and strength levels, ensuring their suitability for demanding applications.
Key Features:
Material Composition: ASTM A671 pipes are made from carbon steel plates, which may include varying amounts of carbon and iron. The carbon content typically ranges from 0.25% to 0.30%, providing a balance of strength and ductility.
Mechanical Properties: These pipes offer excellent mechanical strength, making them suitable for high-pressure applications. They exhibit high tensile strength and yield strength, ensuring structural integrity under demanding conditions.
Corrosion Resistance: While carbon steel is susceptible to corrosion, ASTM A671 pipes are often coated or lined to enhance their resistance to corrosion, making them suitable for harsh environments.
Temperature Tolerance: ASTM A671 pipes are designed to withstand both atmospheric and lower temperatures, making them ideal for use in environments where temperature fluctuations are common.
Weldability: The electric-fusion-welded process ensures strong and reliable welds, enhancing the overall durability and performance of the pipes.
Applications:
ASTM A671 pipes are widely used in various industries, including:
Oil and Gas: Used for transporting oil, gas, and other fluids over long distances.
Power Generation: Employed in power plant piping systems.
Infrastructure: Utilized in construction projects for water and gas supply.
Chemical Processing: Suitable for various chemical processing applications.
Advantages:
Cost-Effective: Carbon steel is relatively affordable compared to other materials, making ASTM A671 Carbon Steel Pipes a cost-effective solution for many projects.
High Strength and Durability: The combination of carbon steel and the electric-fusion-welded process results in pipes that offer high strength and durability, ensuring long-lasting performance in demanding applications.
Versatility: With various grades and classes available, these pipes can be tailored to meet specific project requirements, providing versatility in application.
Excellent Weldability: The welding process used in ASTM A671 pipes ensures strong and reliable joints, reducing the risk of leaks and failures.
ASTM A671 Steel Pipe in Key Applications in the Oil and Gas Industry
ASTM A671 steel pipes are widely recognized for their strength, reliability, and corrosion resistance, making them essential components in the oil and gas industry. Their ability to withstand high-pressure and low-temperature conditions makes them an ideal choice for a variety of critical applications within the sector.
Oil and Gas Pipeline Construction: ASTM A671 steel pipes are commonly used in the construction of pipelines that transport crude oil, natural gas, and refined products across vast distances. These pipes offer high tensile strength, ensuring the integrity of the pipeline even in challenging terrains and extreme environments.
Deepwater and Offshore Applications: In offshore oil drilling and deepwater pipelines, ASTM A671 steel pipes are critical due to their ability to resist corrosion and endure the harsh conditions of underwater environments. The pipes’ robust nature ensures the safety and efficiency of deep-sea oil and gas extraction.
High-Pressure Systems: The high-pressure resistance of ASTM A671 steel pipes makes them ideal for high-pressure oil and gas transportation systems. Whether it’s natural gas transmission or transporting refined products, these pipes can handle the pressure of large-scale industrial applications.
Refinery and Chemical Plants: In addition to transportation, ASTM A671 steel pipes are also used in oil refineries and chemical plants, where they are subjected to high temperatures and corrosive chemicals. Their durability ensures consistent performance and longevity under these demanding conditions.
Enhanced Safety in Harsh Environments: The oil and gas industry often operates in extreme climates, from frozen tundras to scorching deserts. ASTM A671 steel pipes are designed to maintain their strength and performance even in these harsh environments, providing safety and reliability in the most challenging conditions.
Technical Advantages and Performance Comparison of ASTM A671 Steel Pipes
ASTM A671 steel pipes are widely praised for their superior performance in various industrial applications, particularly in high-pressure and low-temperature environments like those found in the oil and gas industry. Here’s an analysis of their key technical advantages and a comparison with other common materials used in similar applications.
1. High Strength and Durability
ASTM A671 steel pipes are manufactured using pressure vessel-quality plates that are welded together to create robust, high-strength pipes. The welding process ensures that the pipes have excellent mechanical properties, including high tensile and yield strength, which makes them resistant to pressure and physical stress.
Comparison:
VS. Carbon Steel (Non-Standard): While general carbon steel may have adequate strength, ASTM A671 offers superior tensile strength, making it more suitable for high-pressure applications.
VS. Stainless Steel: While stainless steel offers better corrosion resistance, it tends to be more expensive. ASTM A671 provides a balance between strength, durability, and cost-effectiveness for high-pressure use in various sectors, including oil and gas.
2. Corrosion Resistance
One of the standout features of ASTM A671 steel pipes is their enhanced corrosion resistance. Though carbon steel is naturally more prone to corrosion, ASTM A671 pipes can be coated or lined to resist rust and corrosion from chemicals, water, and extreme environmental conditions.
Comparison:
VS. Carbon Steel (Non-Coated): Standard carbon steel without coatings is vulnerable to corrosion, especially in harsh conditions. ASTM A671, however, offers more robust protection against corrosion.
VS. Alloy Steel: While alloy steels often have good corrosion resistance, ASTM A671 steel pipes are specifically designed for durability in high-pressure pipelines and are more cost-effective.
3. Weldability and Fabrication
The electric-fusion-welding process used to fabricate ASTM A671 steel pipes ensures that the joints are strong and reliable. This welding method produces fewer defects, which improves the overall performance of the pipes under high-pressure and temperature conditions.
Comparison:
VS. ERW Steel Pipes: Compared to Electric Resistance Welded (ERW) steel pipes, ASTM A671’s electric-fusion welding offers more reliable and durable joints, making it better for applications that involve high pressure or potentially hazardous materials.
VS. Seamless Pipes: Seamless pipes have no welded joints and are generally stronger. However, ASTM A671 offers a cost-effective alternative with competitive strength and reliability, especially in larger-scale pipeline applications.
4. Temperature and Pressure Resistance
ASTM A671 steel pipes are designed to perform effectively in both low-temperature and high-pressure environments. The pipes can be used in temperatures as low as -20°C and still maintain their structural integrity, making them highly suitable for deepwater and offshore oil pipelines, where extreme environmental conditions prevail.
Comparison:
VS. LSAW Steel Pipes: Longitudinally Submerged Arc Welded (LSAW) steel pipes are better for certain high-pressure applications due to their thicker walls. However, ASTM A671 provides a good balance of strength and pressure resistance, suitable for most medium to high-pressure systems.
VS. PVC/Plastic Pipes: PVC or other plastic pipes offer excellent resistance to corrosion and are lighter, but they are not suitable for high-pressure applications. ASTM A671 steel pipes are far more durable and reliable in environments where high pressure is involved.
5. Cost Efficiency
While ASTM A671 steel pipes are made from high-quality carbon steel, their production costs are relatively lower compared to alloys and seamless pipes. They provide a cost-effective solution for industries requiring high-strength, corrosion-resistant pipes, particularly in large-scale transportation projects like pipelines.
Comparison:
VS. Stainless Steel: Stainless steel offers excellent corrosion resistance but is much more expensive than ASTM A671 steel pipes. ASTM A671 provides a balance between performance and cost.
VS. Composite Materials: Composite materials offer certain advantages in terms of weight and corrosion resistance but lack the pressure tolerance that ASTM A671 pipes provide. Composite pipes are also more expensive than ASTM A671.
6. Versatility in Application
Due to the wide variety of available grades and customizations, ASTM A671 steel pipes are versatile and adaptable to different industrial applications, including oil and gas transportation, chemical processing, and power generation.
Comparison:
VS. Alloy Steel: Alloy steel is often used in specialized applications but tends to be more costly and harder to fabricate. ASTM A671 provides a versatile, more affordable solution without sacrificing essential performance.
VS. Galvanized Steel: Galvanized steel pipes have better initial corrosion resistance but are more prone to degradation over time compared to ASTM A671 pipes, especially in high-pressure environments.
How to Select ASTM A671 Steel Pipes and Ensure Quality Control to Meet International Standards?
When selecting ASTM A671 steel pipes, it’s crucial to consider the specific industry requirements, environmental conditions, and quality control standards. Here are the key steps in choosing and ensuring the quality of these pipes:
1. Selecting the Right Specifications and Sizes
The size, wall thickness, grade, and material analysis of ASTM A671 steel pipes should be chosen based on the specific project requirements. The factors to consider when selecting pipes include:
Outer Diameter and Wall Thickness: The pipe size should be determined based on the type of transported medium, pressure requirements, and transportation distance.
Operating Pressure and Temperature: The working pressure and temperature of the pipe should meet the actual operating conditions to ensure the pipe can withstand high pressure or low temperature environments.
Environmental Conditions: For pipes exposed to corrosive environments, it’s advisable to choose steel pipes with additional corrosion-resistant coatings.
2. Choosing the Right Material Grade
ASTM A671 steel pipes come in various analyses and strength levels. The appropriate material grade should be selected based on the pipe’s pressure and temperature requirements. For high-pressure applications, higher strength material grades should be chosen to ensure the pipe’s performance under demanding conditions.
3. Quality Control and Testing
To ensure ASTM A671 steel pipes meet international standards and maintain high quality, the following key quality control steps should be followed:
Raw Material Inspection: Ensure that the raw materials used for production comply with ASTM A671 standards. Materials should be verified for chemical composition and mechanical properties to ensure they meet the required strength and corrosion resistance.
Manufacturing Process Control: Strictly control the welding process during production. The electric-fusion-welding (EFW) method should be used to guarantee the strength and quality of the welds. Non-destructive testing (NDT), such as radiographic or ultrasonic inspections, should be performed to ensure the integrity of the welds.
Pipe Size and Wall Thickness Measurement: Ensure the pipe’s outer diameter, inner diameter, and wall thickness meet international standards and customer requirements. Accurate measuring tools should be used for testing.
Physical Performance Testing: Each batch of steel pipes should undergo tensile testing, hardness testing, and impact testing to verify that they meet the mechanical properties specified in ASTM A671.
Corrosion Resistance Testing: Steel pipes should undergo salt spray testing, acid immersion testing, and other corrosion resistance tests to ensure they can perform in harsh environments.
Final Inspection and Certification: Before leaving the factory, a thorough inspection should be conducted, and a certificate of compliance should be issued, covering chemical composition, mechanical properties, size accuracy, and other indicators to confirm the pipe meets ASTM A671 standards.
4. Ensure International Certifications
To guarantee that the pipes meet international standards, manufacturers should obtain relevant certifications, such as ISO 9001 for quality management and API 5L certification for pipeline materials. These certifications ensure that the production process and product quality consistently meet international standards.
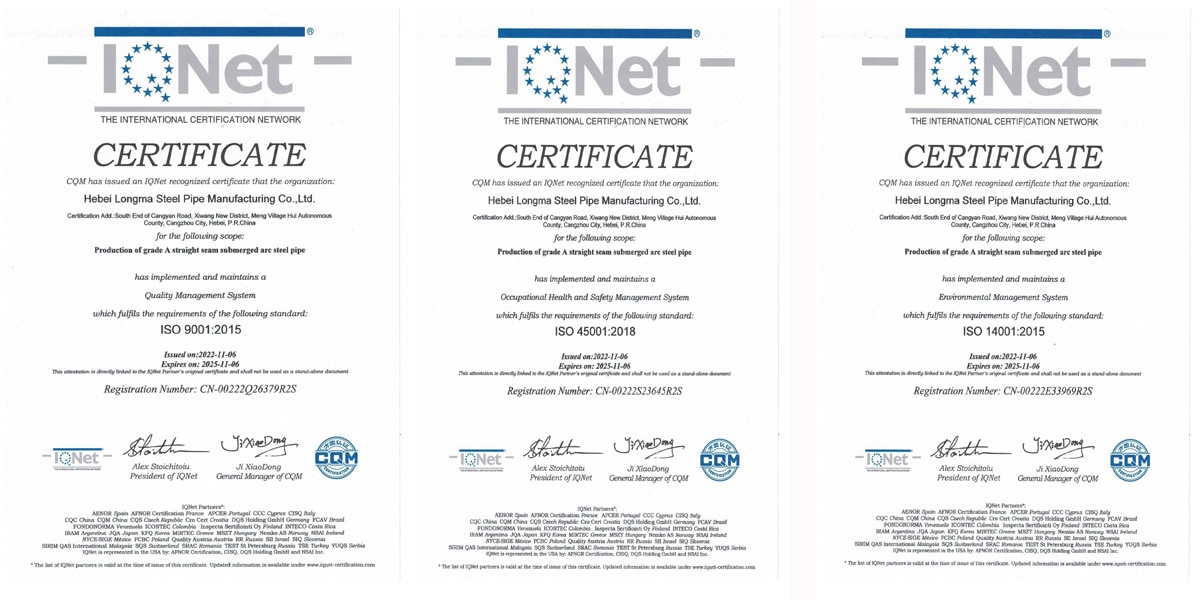
Future Development Trends of ASTM A671 Steel Pipes
ASTM A671 steel pipes are renowned for their exceptional performance and are widely used in industries such as oil and gas, power generation, and chemical processing. Looking ahead, the development trends for ASTM A671 steel pipes are expected to focus on the following areas:
1. Enhanced Performance: As industrial applications demand higher material performance, ASTM A671 steel pipes are anticipated to evolve towards greater strength, higher temperature resistance, and improved corrosion resistance to meet more stringent operating conditions.
2. Customization and Multifunctionality: With increasing customer demand for diverse and personalized products, ASTM A671 steel pipes are expected to offer more customized solutions and services to meet specific application requirements.
3. Environmental Sustainability: In response to growing environmental concerns, the production and use of ASTM A671 steel pipes are likely to emphasize the adoption of eco-friendly materials and processes to minimize environmental impact.
4. Smart Manufacturing: The integration of smart manufacturing technologies is expected to make the production of ASTM A671 steel pipes more automated and intelligent, enhancing production efficiency and product quality.
5. Market Demand Growth: According to QYResearch, the global alloy seamless steel pipe market is projected to grow from $6.821 billion in 2024 to $9.79 billion by 2031, with a compound annual growth rate (CAGR) of 5.3%.
As the demand for high-performance materials continues to grow across various industries, ASTM A671 steel pipes will play an increasingly vital role in ensuring the reliability and safety of critical infrastructure. With advancements in performance, customization, sustainability, and manufacturing technologies, these pipes are well-positioned to meet the challenges of tomorrow’s industrial needs!
At HeBei LongMa Steel Pipe Manufacturing Co.,Ltd, we are committed to providing high-quality ASTM A671 steel pipes that adhere to international standards and meet the unique requirements of each application. Should you have any questions or need expert advice on steel pipes, feel free to contact us anytime. Our team is always here to help you find the best solutions for your projects!