ASTM A672 steel pipes are widely used in industries such as oil and gas transmission and water treatment, making it crucial to ensure their quality meets international standards. In the previous article, we discussed the standard specifications and applications of ASTM A672 steel pipes. In this article, we will focus on the quality control measures and inspection methods during production, ensuring that every pipe meets international standards and satisfies customer requirements!
Overview of ASTM A672 Steel Pipes
ASTM A672 steel pipes are manufactured to meet the ASTM A672 standard and are primarily used in high-pressure and high-temperature environments, including oil and gas transmission, energy pipelines, and water treatment systems. These pipes are produced using specific manufacturing processes to ensure excellent strength, corrosion resistance, and pressure resistance, making them widely used in critical infrastructure projects like oil and gas transmission and cross-country pipelines.
Performance Features:
High Strength and Pressure Resistance: ASTM A672 steel pipes are made with specialized materials and welding techniques, allowing them to withstand the high-pressure demands of fluid transportation and ensure the safe operation of pipeline systems.
Corrosion Resistance: With corrosion-resistant treatments, ASTM A672 steel pipes perform well in harsh environments, especially in wet or corrosive conditions.
Excellent Weldability: The pipes are designed with appropriate welding materials and techniques, ensuring that the welded joints match the strength of the pipe body, ensuring overall performance stability.
Strong Adaptability: Suitable for low, high, and high-pressure environments, these pipes effectively resist the impact of different media on the pipeline.
Quality Control Process of ASTM A672 Steel Pipes
The quality control process of ASTM A672 steel pipes ensures that every pipe meets strict quality standards during production and complies with international requirements. Below are the key quality control steps involved:
1. Raw Material Inspection: Before production, all raw materials (such as steel plates and pipe billets) undergo strict quality checks to ensure their chemical composition and mechanical properties meet ASTM A672 standards. The source of raw materials is usually certified to ensure reliability.
2. Dimensional and Visual Inspection: During the pipe formation process, the dimensions and appearance are first checked to ensure the pipe’s outer diameter, wall thickness, length, and other parameters conform to specifications. Any non-compliant sections are marked and corrected.
3. Welding Quality Control: The welding process is closely monitored to ensure the weld strength matches the pipe body. Non-destructive testing methods (such as X-ray inspection or ultrasonic testing) are used to check the integrity of the welds, ensuring there are no potential defects.
4. Mechanical Property Testing: ASTM A672 steel pipes undergo a series of mechanical property tests, including tensile strength, yield strength, and elongation. This ensures that each pipe’s mechanical performance meets the requirements of ASTM standards.
5. Corrosion Resistance Testing: After surface corrosion protection treatment, the pipes undergo corrosion resistance testing to ensure they can effectively withstand corrosion in various environments, thus extending their service life.
6. Pressure Testing: Steel pipes are subjected to high-pressure water tests to evaluate their pressure resistance. This test ensures that the pipes can withstand the high-pressure fluids in the transportation process.
7. Final Inspection and Marking: In the final production stage, comprehensive inspections are carried out, including checks on appearance, dimensions, weld quality, and mechanical properties. Compliant products are marked and accompanied by quality reports to confirm that each pipe meets the required standards.
Inspection Methods of ASTM A672 Steel Pipes
To ensure that ASTM A672 steel pipes meet stringent quality standards and perform reliably in various applications, a series of inspection methods are employed. Below are the key inspection methods:
Chemical Composition Inspection: The raw materials for the steel pipes undergo chemical composition analysis to ensure they meet the requirements of the ASTM A672 standard. Common inspection methods include spectrographic analysis and spark emission direct-reading analysis to verify the content of key elements (such as carbon, manganese, silicon, chromium, etc.).
Dimensional Inspection: The steel pipes are inspected for outer diameter, wall thickness, length, and other critical dimensions to ensure they meet the design specifications. Common inspection methods include caliper measurement, ultrasonic measurement, and laser measurement.
Welding Quality Inspection: The welded areas undergo non-destructive testing (NDT), with common methods including X-ray inspection, ultrasonic testing, magnetic particle testing, and penetrant testing. These methods are used to detect any cracks, porosity, inclusions, or other defects in the welds to ensure welding quality meets the standard.
Mechanical Property Inspection: Mechanical property tests such as tensile strength, yield strength, and elongation are conducted. Common inspection methods include tensile testing, bend testing, and hardness testing to ensure the mechanical properties of the pipes comply with the ASTM A672 standard.
Hydrostatic Test: To check the pressure resistance of the steel pipes, a hydrostatic test is performed. The pipes are subjected to pressures higher than their intended use to ensure they can safely withstand high-pressure conditions. The hydrostatic test is typically carried out using a liquid pressure testing machine.
Corrosion Resistance Inspection: The corrosion resistance of the steel pipes is tested through accelerated corrosion tests. Common methods include salt spray tests and acid mist tests, which simulate harsh environmental exposure to assess the pipes’ resistance to corrosion.
Hardness Testing: Hardness testing is conducted to determine the hardness level of the steel pipes using methods like Brinell hardness, Rockwell hardness, or Vickers hardness tests. These tests evaluate the pipes’ wear resistance and ability to resist deformation.
Final Inspection and Marking: During the final stage of production, comprehensive visual inspections, marking, and dimensional checks are conducted to ensure the pipes meet customer requirements and international standards. Compliant products are accompanied by quality reports and relevant certificates.
International Standards and Certifications for ASTM A672 Steel Pipes
ASTM A672 steel pipes are produced in accordance with the standards set by the American Society for Testing and Materials (ASTM), which outline the chemical composition, mechanical properties, welding quality, and corrosion resistance requirements. These pipes conform to various international standards and certifications, ensuring their widespread acceptance and use in global markets. Below are the main international standards and certifications related to ASTM A672 steel pipes:
ASTM A672 Standard: The ASTM A672 standard is issued by ASTM and specifically covers steel pipes used for high-pressure transmission and energy pipelines. This standard specifies detailed requirements for chemical composition, mechanical properties, dimensional tolerances, and welding standards. ASTM A672 steel pipes are commonly used in applications involving high-pressure and high-temperature environments, particularly in the oil, gas, and energy sectors.
ISO 9001 Quality Management System Certification: Many manufacturers of ASTM A672 steel pipes are ISO 9001 certified. ISO 9001 is an international standard for quality management systems that requires organizations to implement continuous improvements in product design, production, quality control, and delivery. Companies with ISO 9001 certification demonstrate a commitment to maintaining stable product quality and meeting customer expectations.
ISO 14001 Environmental Management System Certification: ISO 14001 is an international standard for environmental management systems. Many producers of ASTM A672 steel pipes also hold ISO 14001 certification, which requires companies to take measures to reduce their environmental impact and comply with environmental regulations during production.
API 5L Certification: Although API 5L primarily pertains to steel pipes used in the oil and gas industry, many manufacturers of ASTM A672 steel pipes also hold API 5L certification. This certification ensures that the steel pipes meet specific mechanical properties and corrosion resistance requirements, ensuring their safe use in oil and gas transportation and other energy pipelines.
CE Certification (European Market): ASTM A672 steel pipes sold in the European market may need to comply with the European CE certification requirements. The CE mark indicates that the product meets the health, safety, and environmental protection standards required by the European Economic Area, allowing it to be freely traded within the EU market.
NACE Certification: NACE (National Association of Corrosion Engineers) certification is awarded for the corrosion resistance of steel pipes. Many manufacturers of ASTM A672 steel pipes hold NACE certification, proving that their pipes have excellent corrosion resistance, making them suitable for use in harsh environments.
UL Certification (United States): For certain projects requiring compliance with U.S. national standards, ASTM A672 steel pipes may need to be UL certified. While UL certification is primarily associated with electrical products, some pipeline systems and materials also require UL testing to ensure their safety and suitability for specific applications.
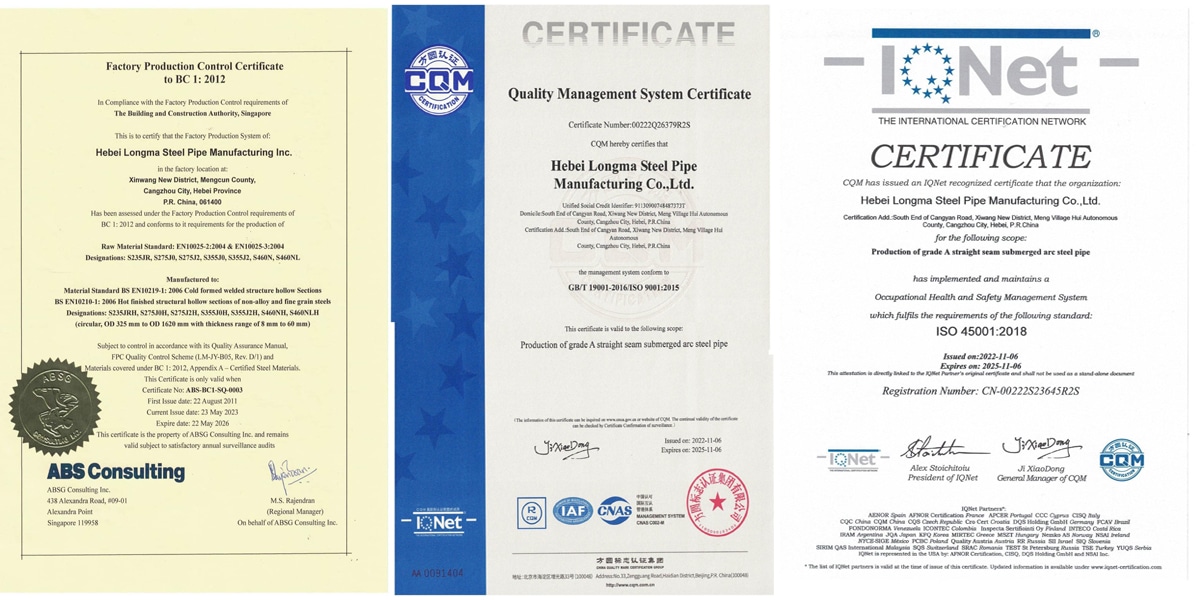
Challenges and Solutions in Quality Control and Inspection of ASTM A672 Steel Pipes
Quality control and inspection of ASTM A672 steel pipes are critical for ensuring product reliability and compliance with industry standards. However, there are several challenges faced during the manufacturing and inspection processes. Below are some common challenges and their corresponding solutions:
1. Challenge: Variability in Raw Material Quality
Solution: To ensure consistency in the final product, raw materials used in the production of ASTM A672 steel pipes should undergo rigorous testing before manufacturing begins. Implementing a strict supplier qualification process and requiring material certification from trusted vendors can minimize the risks associated with variability. Additionally, conducting real-time chemical composition analysis using advanced spectrometers can ensure that the materials used meet the required specifications.
2. Challenge: Complex and Strict Inspection Standards
Solution: ASTM A672 steel pipes must meet various stringent inspection standards, such as dimensional accuracy, mechanical strength, and welding integrity. To address this, companies can adopt automated inspection systems equipped with high-precision sensors and cameras to reduce human error. Additionally, investing in advanced non-destructive testing (NDT) technologies, such as ultrasonic testing and X-ray inspection, can provide more reliable results and improve efficiency during inspections.
3. Challenge: Weld Quality Control
Solution: Achieving high-quality welds is essential for the integrity and safety of the pipes. A common challenge is ensuring the absence of defects such as cracks, porosity, and undercuts in the welds. The solution is to implement continuous in-process inspection methods like ultrasonic or eddy current testing to monitor weld quality in real time. Additionally, using qualified welding professionals and providing ongoing training on advanced welding techniques ensures that the welding process remains controlled and effective.
4. Challenge: Pressure Testing and Hydrostatic Testing Failures
Solution: One of the most critical quality assurance tests for steel pipes is the hydrostatic pressure test. Failures in pressure testing can occur due to manufacturing defects, incorrect pipe dimensions, or improper sealing. To mitigate this, regular calibration and maintenance of testing equipment are essential. Moreover, implementing a multi-step pressure testing process, where pipes are subjected to incremental pressure before the final test, can help detect early-stage failures and reduce the likelihood of catastrophic failure.
5. Challenge: Corrosion Resistance and Environmental Conditions
Solution: Steel pipes, especially those used in oil, gas, and water transportation, are vulnerable to corrosion, which can compromise their performance. To address this, a robust anti-corrosion coating process, such as hot-dip galvanizing or epoxy coating, should be applied. Additionally, performing accelerated corrosion tests like salt spray testing helps assess the pipes’ ability to withstand extreme environmental conditions. Periodic maintenance and re-coating can further extend the lifespan of the pipes.
6. Challenge: Maintaining Consistent Dimensional Accuracy
Solution: Maintaining precise dimensional accuracy throughout the manufacturing process is crucial for ensuring the proper fit and functionality of the pipes. Automated machinery with precise control systems can be used to monitor and adjust dimensional accuracy in real-time. Using laser measurement technology and computer-aided design (CAD) software for initial design and post-production verification also ensures high levels of dimensional consistency.
7. Challenge: Timely Delivery of Inspection Results
Solution: The timely delivery of inspection results is vital for the production timeline and overall project deadlines. To speed up the process, many manufacturers are moving toward digital inspection methods and automated data collection systems. This allows inspection data to be quickly analyzed and processed, resulting in faster decision-making and reducing production delays.
8. Challenge: Managing Large Volume of Data
Solution: The inspection and quality control of ASTM A672 steel pipes generate a large volume of data, including test results, dimensional checks, and performance metrics. Managing this data effectively can be a challenge. The solution is to implement a centralized quality management system (QMS) with cloud-based storage, allowing for easy access, analysis, and sharing of data across departments. The integration of real-time monitoring and data analytics tools also enhances decision-making by providing insights into trends and potential quality issues.
The quality control and inspection processes for ASTM A672 steel pipes come with several challenges, but through advanced technologies, strict control measures, and efficient management systems, manufacturers can ensure that the pipes meet industry standards and customer requirements. With the continuous advancement of technology and industry development, we believe that quality control and inspection methods will continue to innovate to ensure the stability and reliability of steel pipes in various demanding environments!
If you’re interested in learning more about other types of pipes or related products’ quality control, feel free to leave a comment telling us what you’d like to know. We’ll provide you with more detailed information and in-depth analysis!