Among the various types of steel pipes, LSAW steel pipes (Longitudinal Submerged Arc Welded pipes) are highly sought after for their exceptional strength, durability, and versatility in industrial applications. Whether for oil and gas pipelines, structural projects, or marine engineering, selecting a reliable LSAW Steel Pipe Manufacturer is critical to ensuring project quality and efficiency. However, with so many LSAW Pipe Manufacturers in the market, how do you make the right choice? This article will guide you through the process of identifying the best LSAW Pipe Manufacturer and finding trustworthy LSAW Steel Pipe Suppliers for your needs!
Manufacturing Process of LSAW Steel Pipes
1. The Production Process of LSAW Steel Pipes
LSAW (Longitudinal Submerged Arc Welded) steel pipes are renowned for their high strength and excellent quality control, making them the preferred choice for demanding engineering projects. The production process includes the following key steps:
Steel Plate Preparation: High-quality steel plates, often meeting international standards such as API 5L or ASTM, are selected for LSAW pipe production. Before manufacturing, the plates undergo ultrasonic testing (UT) to ensure they are free from internal cracks, porosity, or other defects.
Plate Forming: The steel plates are formed into a pipe shape using the JCOE method. This involves sequential bending into J, C, and O shapes, followed by final forming into a pipe body. This process ensures precise diameters, excellent roundness, and dimensional accuracy.
Welding Process: Both internal and external seams are welded using submerged arc welding (SAW). Internal seams are welded first, followed by the external seams. This technique ensures weld quality comparable to the base material, providing high reliability and superior mechanical strength.
Heat Treatment and Expansion: After welding, the pipes are heat-treated to eliminate residual stress from the welding process. Mechanical expansion is then performed to further enhance dimensional precision and surface quality.
Inspection and Acceptance: The finished pipes undergo stringent inspections, including ultrasonic testing, X-ray inspection, and hydrostatic testing, to ensure their strength, sealing performance, and compliance with standards. Finally, surface treatments such as epoxy coating or galvanization are applied to prolong their service life.
2. Advantages of LSAW Steel Pipes
High Strength and Excellent Mechanical Properties: The weld strength of LSAW pipes is nearly equivalent to that of the base material, making them suitable for high-pressure and harsh environmental conditions, particularly in long-distance and high-strength pipeline transportation.
Reliable Weld Quality: Submerged arc welding produces deep, uniform welds with minimal defects, making LSAW pipes ideal for high-safety and durability projects.
Superior Dimensional Accuracy: Through advanced expansion processes, LSAW pipes achieve uniform diameter, roundness, and wall thickness, meeting the strict requirements of high-standard projects.
Wide Range of Applications: LSAW pipes are widely used in oil and gas transportation, bridge construction, and offshore engineering, offering exceptional adaptability and long-term reliability.
3. Comparison with Other Types of Steel Pipes
When compared to other types of steel pipes, LSAW pipes exhibit distinct advantages in terms of manufacturing processes, performance, and applications:
First, compared to ERW pipes (Electric Resistance Welded pipes), LSAW pipes use submerged arc welding, resulting in stronger and more stable weld quality. This makes LSAW pipes suitable for high-pressure and high-strength applications, while ERW pipes, with thinner welds, are generally used in lightweight applications such as water pipes or general structural uses.
Second, compared to spiral welded pipes (SSAW), LSAW pipes have shorter weld lengths, reducing the likelihood of defects and ensuring more reliable quality. Although SSAW pipes are more cost-effective, their strength and sealing performance are inferior, making them more suitable for low-pressure or non-critical engineering projects.
How to Choose the Right LSAW Steel Pipe Manufacturer?
Why Choosing the Right LSAW Steel Pipe Manufacturer is Critical?
LSAW (Longitudinal Submerged Arc Welded) steel pipes play a vital role in demanding projects, such as oil and gas pipelines, offshore engineering, and large-scale construction. Selecting a reliable LSAW steel pipe manufacturer ensures not only product quality but also reduces project risks and enhances efficiency. Below are the key factors to consider:
1. Manufacturer’s Certifications and Credentials
International Certifications: A high-quality LSAW steel pipe manufacturer should hold relevant international certifications, such as ISO 9001 for quality management and API 5L for pipeline standards. These certifications guarantee adherence to industry standards.
Industry Experience: Manufacturers with years of experience, especially those with proven success in large-scale projects, provide a more reliable partnership.
2. Advanced Technology and Equipment
State-of-the-Art Equipment: Ensure the manufacturer employs advanced JCOE forming machines and submerged arc welding technology, enabling precise pipe forming and superior weld quality.
Inspection Capabilities: The manufacturer should be equipped with complete testing systems, including ultrasonic flaw detectors, X-ray inspection devices, and hydrostatic testing facilities, to ensure the pipes meet quality standards.
3. Product Quality and Performance
Material Selection: The quality of raw steel significantly impacts the final product. Verify whether the manufacturer sources materials from reliable suppliers that comply with international standards such as API and ASTM.
Weld Quality: The weld quality of LSAW pipes directly affects their strength and durability. Manufacturers should utilize advanced submerged arc welding to ensure weld seams have properties comparable to the base material.
Dimensional Precision: High accuracy in diameter, roundness, and wall thickness is critical, especially for projects with stringent requirements.
4. Production Capacity
Scale and Output: Ensure the manufacturer has sufficient production capacity to meet project demands, particularly for large-scale projects requiring bulk supply.
Delivery Time: Evaluate whether the manufacturer can deliver on time, especially for projects with tight schedules, as timely delivery is crucial for smooth project execution.
5. Customer Service and Technical Support
Customization Capability: A good manufacturer should offer tailored solutions, such as non-standard sizes, special coatings, or specific materials to suit project needs.
Technical Assistance: A professional technical team should provide support in areas like product selection, installation guidance, and after-sales service, ensuring a seamless experience for the customer.
6. Comparing with Other Suppliers
Price and Value for Money: Compare multiple manufacturers, focusing not only on price but also on the overall value offered. Avoid choosing substandard products based solely on low prices.
Market Reputation: Investigate the manufacturer’s reputation and customer feedback. Look for LSAW Steel Pipe Manufacturers with a proven track record and positive reviews in the industry.
Overview of The Main Application Fields of LSAW Steel Pipes
1. Oil and Gas Pipelines
LSAW steel pipes are widely used in long-distance oil and gas transportation pipelines due to their high strength and reliable welding performance. These projects often require exceptional pressure resistance, sealing capabilities, and corrosion resistance, which LSAW pipes can meet.
Features: High-pressure resistance with excellent anti-corrosion properties.
Typical Projects: Cross-border oil pipelines, deep-sea gas pipelines.
2. Offshore Engineering
In offshore engineering, LSAW steel pipes are commonly utilized as subsea pipelines or platform support structures. Their superior mechanical properties and resistance to environmental corrosion make them ideal for the challenges of seawater, high salinity, and high pressure.
Features: Excellent tensile strength, corrosion resistance, and long service life.
Applications: Subsea oil and gas pipelines, offshore platform pillars.
3. Construction and Infrastructure
LSAW steel pipes are used in large construction and infrastructure projects for structural supports, bridge foundations, and core supports in high-rise buildings. Their precise dimensions and high strength make them a preferred material for such projects.
Features: Accurate dimensions and outstanding compressive strength.
Typical Examples: High-speed rail bridge supports, structural frames for large stadiums.
4. Water Resource Projects
LSAW steel pipes are often used in water supply and drainage systems for transporting high-pressure water, especially in environments requiring immense pressure resistance. Their inner and outer surfaces can be specially coated to enhance corrosion resistance.
Features: High-pressure handling capacity with excellent anti-corrosion treatments.
Applications: Urban water supply pipelines, flood discharge pipelines for large reservoirs.
5. Energy Sector
LSAW steel pipes are extensively used in various energy applications, including high-temperature pipes in thermal power plants and critical pipelines in nuclear power plants. Their high-temperature resistance and long service life are key advantages.
Features: Heat resistance, high-pressure endurance, and extended lifespan.
Applications: Boiler pipelines in power plants, cooling water pipelines in nuclear power plants.
6. Heavy Industry and Manufacturing
In chemical plants and large equipment manufacturing, LSAW steel pipes are used to transport corrosive liquids or gases or as part of equipment structures.
Features: Exceptional corrosion resistance and fatigue performance.
Applications: Chemical raw material pipelines, supporting frameworks for heavy machinery.
Quality Control and Standards for LSAW Steel Pipes
1. Importance of Quality Control for LSAW Steel Pipes
LSAW (Longitudinal Submerged Arc Welded) steel pipes are widely used in industries such as oil and gas, construction, and water management due to their superior strength and reliability. To ensure safety and stability in high-pressure, high-temperature, and harsh environments, rigorous quality control is essential.
2. Quality Control Stages for LSAW Steel Pipes
(1) Raw Material Inspection
Steel Plate Quality: The raw steel plates must comply with international standards such as API, ASTM, or EN, and undergo chemical composition analysis and mechanical performance testing to ensure they meet the required tensile strength, yield strength, and ductility.
Surface Defect Detection: Visual inspections and ultrasonic testing are used to check the steel plate’s surface for cracks, dents, or other defects.
(2) Forming and Welding Control
JCOE Forming Process: LSAW steel pipes are formed using the JCOE (J-ing, C-ing, O-ing, and Expanding) process, which involves multiple mechanical presses to form the steel plate into an accurate pipe shape, ensuring the pipe’s roundness and dimensional precision.
Welding Process Control: The welding quality directly impacts the strength and reliability of the steel pipe. LSAW steel pipes use submerged arc welding (SAW) technology with multiple weld passes to ensure the weld strength matches the base material. The welding parameters, such as current, voltage, and welding speed, are closely monitored in real-time.
(3) Non-Destructive Testing
Ultrasonic Testing: Used to detect cracks, voids, and other internal defects in the welds and base material.
X-Ray Testing: A 100% X-ray inspection of the welds is performed to ensure there are no defects in the welded areas.
Magnetic Particle Inspection: Used to detect fine surface cracks or imperfections on the pipe’s surface and near-surface areas.
(4) Hydrostatic Testing: Each LSAW steel pipe undergoes a hydrostatic test to verify its pressure sealing and pressure-bearing capacity under working conditions.
(5) Anti-Corrosion and Coating Treatment: Depending on the specific application, the internal and external surfaces of the steel pipe may undergo anti-corrosion treatments (such as epoxy coating or 3PE coating) to enhance corrosion resistance and extend service life.
3. Standards for LSAW Steel Pipes
LSAW steel pipe production must comply with the following common international standards:
(1) Standards for Oil and Gas Transmission
API 5L: Applicable to pipelines for oil and gas transmission, with two grades: PSL1 and PSL2, where PSL2 has higher requirements.
ISO 3183: The international standard for steel pipes for the transportation of oil and gas, similar to API 5L.
(2) Structural Standards
ASTM A252: Suitable for piling steel pipes.
EN 10219: Applicable for cold-formed steel pipes used in structural applications.
(3) Anti-Corrosion Coating Standards
ISO 21809: Standard for external corrosion protection coatings for pipelines in the oil and gas industry.
DIN 30670: Standard for polyethylene coatings for corrosion protection.
4. Summary of the Importance of Quality Control and Standards
Through strict quality control and adherence to international standards, LSAW steel pipes can ensure:
High Strength and Durability: Meeting the requirements of high-pressure, high-temperature, and corrosive environments.
Reliability and Safety: Reducing the risk of pipeline failure and enhancing project stability.
Consistency and Cost-effectiveness: High-quality pipes reduce maintenance costs and improve economic benefits.
Market Trends and Future Development of LSAW Steel Pipes
1. Current Market Overview of LSAW Steel Pipes
LSAW (Longitudinal Submerged Arc Welded) steel pipes are known for their high performance and reliability, widely used in oil and gas transportation, large-scale infrastructure construction, and water resource projects. In recent years, the demand for LSAW steel pipes has shown steady growth, driven by industrialization and urbanization worldwide.
Key Market Drivers
Increasing global energy demand, especially for oil and natural gas projects.
Infrastructure upgrades, such as bridges, buildings, and port constructions, requiring high-strength steel pipes.
Advances in offshore engineering and deep-sea resource development, which rely heavily on LSAW steel pipes.
2. Key Factors Influencing the Market
(1) Technological Advancements
The continuous optimization of LSAW steel pipe production technology, including precision welding, advanced forming equipment, and automated inspection systems, improves product quality and broadens application fields.
The development of anti-corrosion coating technologies extends the service life of LSAW pipes, making them suitable for marine and chemical environments.
(2) Energy Transition and Environmental Regulations
As the world shifts to cleaner energy, the demand for LSAW steel pipes in natural gas pipelines is rapidly growing. These pipelines require high sealing performance and pressure resistance, qualities that LSAW pipes excel at.
Strict environmental policies are pushing manufacturers to adopt greener production processes, enhancing product competitiveness.
(3) Geopolitical Factors and Infrastructure Investments
Initiatives such as the Belt and Road Initiative and global infrastructure investment plans (e.g., the U.S. Infrastructure Investment and Jobs Act) generate significant orders for LSAW steel pipes.
Geopolitical developments significantly influence oil and gas markets, directly impacting the demand for pipeline projects and, consequently, LSAW pipes.
3. Future Trends in the LSAW Steel Pipe Market
(1) Growth in Emerging Markets
Regions such as Asia, Africa, and Latin America are becoming key growth areas due to rapid industrialization and increasing energy needs.
Investments in infrastructure in these emerging economies will further boost the demand for high-quality steel pipes.
(2) Expansion in Deep-Sea and Ultra-Deep-Sea Engineering: Deep-sea oil and gas development requires pipelines capable of withstanding extreme pressure and corrosive environments. LSAW steel pipes, with their superior mechanical properties and anti-corrosion capabilities, are the preferred choice.
(3) Adoption of Sustainable Production Technologies
Manufacturers are expected to focus more on energy-saving and emission-reducing techniques, such as low-carbon steel production and efficient welding processes.
By improving production efficiency and reducing waste, manufacturers can lower costs and enhance market competitiveness.
(4) Integration of Smart and Digital Technologies: Advanced digital production and intelligent inspection systems will be increasingly adopted, enabling real-time monitoring and optimization of the production process to ensure product consistency and quality.
4. Market Outlook for LSAW Steel Pipes
(1) Market Size Forecast
According to market research, the global LSAW steel pipe market is projected to grow at a compound annual growth rate (CAGR) of 4%-6% over the next five years.
Key drivers include demand from the oil and gas sector, infrastructure development, and marine engineering projects.
(2) Industry Competition
Globally, large-scale LSAW steel pipe manufacturers with advanced technology and production capabilities will dominate the market.
Smaller manufacturers can find opportunities by focusing on customized services and regional markets.
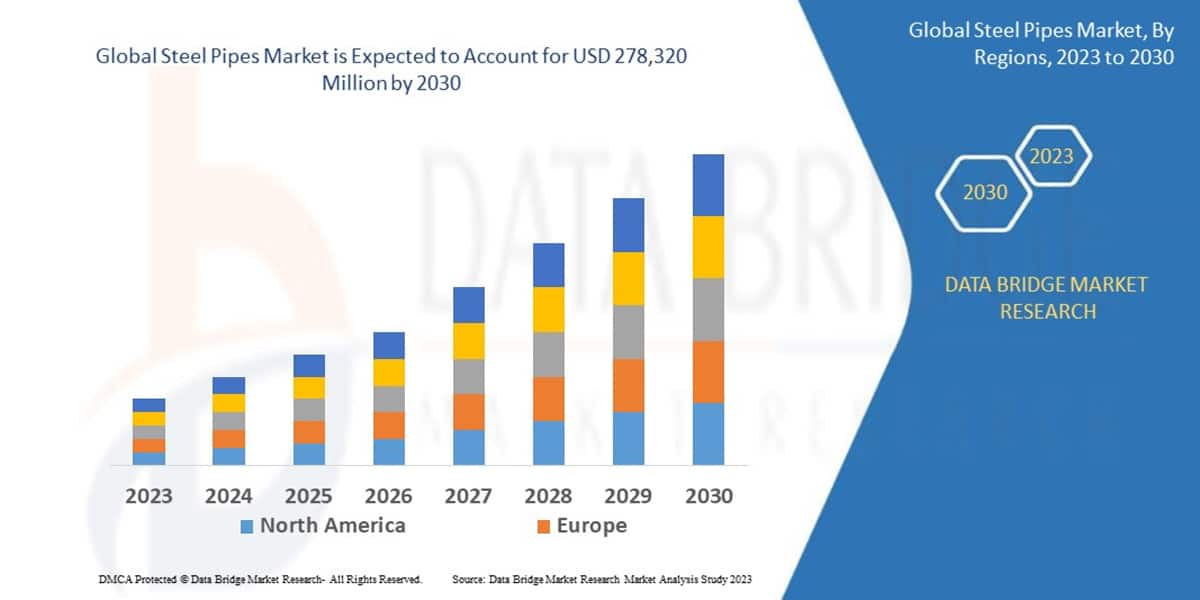
How to Choose The Best LSAW Steel Pipe Manufacturer?
1. Define Your Project Requirements
Before selecting an LSAW steel pipe manufacturer, it is essential to identify your specific project needs, including:
Pipe Specifications: Required dimensions, wall thickness, and length.
Application Environment: Whether it is for high-pressure, corrosive, or deep-sea applications.
Delivery Timeline: Whether the project requires urgent delivery.
Certification Requirements: Ensure compliance with international standards such as API 5L, ASTM A671, etc.
2. Assess the Manufacturer’s Production Capacity and Technical Expertise
(1) Production Scale
Opt for manufacturers with large-scale production capabilities to handle bulk orders efficiently while also accommodating small, customized orders.
Check if their facilities are equipped with advanced production equipment, such as automated welding systems and precision forming machines.
(2) Technical Expertise
Verify whether the manufacturer utilizes cutting-edge LSAW steel pipe production technologies, such as double-sided submerged arc welding and advanced anti-corrosion coating techniques.
Technologically advanced manufacturers are more likely to deliver high-performance and consistent products.
3. Examine Quality Control Systems
(1) Quality Certifications
Ensure the manufacturer holds ISO 9001 certification for quality management and relevant steel pipe certifications such as API and ISO 3183.
These certifications demonstrate compliance with international quality standards.
(2) Testing Capabilities
Confirm whether the manufacturer employs comprehensive testing facilities, including ultrasonic testing, radiographic inspection, and hydrostatic testing equipment.
Robust testing ensures that the products meet technical and safety requirements before delivery.
4. Evaluate Product Variety and Service Capabilities
(1) Product Range
A reputable LSAW steel pipe manufacturer typically offers a diverse range of products, including various sizes, materials, and coatings.
A broad product portfolio indicates strong production capabilities and adaptability to unique customer needs.
(2) Customer Support
Assess whether the manufacturer provides end-to-end customer support, including technical consultation, logistics coordination, and after-sales service.
A professional support team can help address challenges and enhance the overall collaboration experience.
5. Check Industry Reputation and Experience
(1) Manufacturing Experience: Choose a manufacturer with extensive experience in producing LSAW steel pipes. Experienced manufacturers better understand market trends and customer requirements, ensuring reliable products and services.
(2) Customer Feedback: Review customer testimonials and project references, particularly their performance in large-scale projects such as oil and gas pipelines or infrastructure developments.
Successful collaborations with other clients can build trust and confidence.
6. Compare Pricing and Delivery Timelines
(1) Reasonable Pricing
High-quality LSAW steel pipes may come at a premium, but value for money should be a priority.
Avoid selecting manufacturers solely based on low prices, as this could compromise quality.
(2) On-Time Delivery
Ensure the manufacturer can deliver orders within the agreed timeline, particularly for time-sensitive projects.
Delays in delivery can disrupt project schedules and lead to additional costs.
7. Consider Long-Term Collaboration Potential
Look for a manufacturer with whom you can establish a long-term partnership. A quality LSAW steel pipe manufacturer not only delivers high-quality products but also offers flexible services and support as your needs evolve.
Choosing the right LSAW steel pipe manufacturer is a critical step in ensuring the success of your project. By focusing on production capacity, technical expertise, quality assurance, and customer service, you can identify a manufacturer that aligns with your needs. Furthermore, considering manufacturers who comply with international standards and have a proven track record of reliable performance will help ensure a successful partnership. Collaborating with reputable LSAW pipe manufacturers not only guarantees high-quality products but also fosters long-term growth through consistent performance and tailored services. Whether your project demands superior corrosion resistance, high-pressure tolerance, or precision engineering, a trusted LSAW pipe manufacturer can provide solutions that meet and exceed expectations. As global demand for steel pipes continues to grow, working with reliable LSAW steel pipe suppliers will empower you to stay ahead of industry trends, ensuring your projects remain at the forefront of innovation and efficiency.
Hebei Longma Steel Pipe Manufacturing Co., Ltd. (LONGMA), established in 2003, is one of China’s leading ERW/LSAW steel pipe manufacturers. The company specializes in the production of large-diameter, thick-walled, double-sided submerged arc welded steel pipes, LSAW straight seam submerged arc welded steel pipes, and ERW steel pipes. Covering an area of 230,000 square meters, the company’s annual production capacity exceeds 500,000 tons by the end of 2022. We warmly invite you to visit our company and explore potential collaboration opportunities!