With the continuous growth of global energy demand, transnational oil pipelines have become a critical means of international energy transportation, making their construction and maintenance increasingly vital. The choice of pipeline materials plays a decisive role in ensuring the safety, stability, and cost-effectiveness of these pipelines. API 5L steel pipes, widely recognized for their exceptional strength, corrosion resistance, and ability to adapt to complex environments, have emerged as a core material in the construction of transnational oil pipelines. However, the diverse geographical conditions, challenging climates, and long-distance transportation involved in these projects impose higher performance requirements on pipeline materials. This article delves into the practical applications of API 5L steel pipes in transnational oil pipelines and explores their technological advantages in addressing complex environmental challenges!
The Characteristics of API 5L Ateel Pipes
API 5L steel pipes are specifically designed for oil and gas transportation and comply with international standards. They offer a range of excellent characteristics that make them widely used in transnational oil pipelines and energy pipeline construction. The key features include:
Strong Corrosion Resistance: API 5L steel pipes are made with special alloy components and anti-corrosion technologies, providing excellent resistance to corrosion from oil, natural gas, and other media. This ensures a long service life, particularly in harsh environmental conditions.
High Strength and Toughness: These steel pipes are capable of withstanding high pressure, extreme temperatures, and external impacts, ensuring safety and stability during the transportation of oil and gas.
Compliance with International Standards: API 5L steel pipes adhere to the stringent standards set by the American Petroleum Institute (API), ensuring their universal applicability and compliance across different countries and regions. They are the preferred material for international oil and gas transportation projects.
Suitable for Long-Distance Transnational Transportation: Due to their high pressure resistance and corrosion resistance, API 5L steel pipes are widely used in transnational oil pipelines and long-distance oil and gas transportation projects, ensuring the efficient operation of energy pipelines in complex geographic environments.
Excellent Weldability: API 5L steel pipes have good weldability, making it easier to assemble and maintain pipelines, ensuring smooth and safe oil and gas transportation.
The Application of API 5L Steel Pipes in Transnational Oil Pipelines
Transnational oil pipelines are critical infrastructure for global energy transportation, responsible for transporting oil and natural gas from production areas to consumer markets. Since these pipelines span different countries and regions, they encounter complex geographic environments, climate variations, and technical requirements. Therefore, the selection of pipeline materials must consider factors such as corrosion resistance, strength, toughness, and environmental adaptability. API 5L steel pipes, with their excellent properties, have become the ideal choice to meet these demands.
Challenges and Requirements of Transnational Oil Pipelines
Transnational oil pipelines face several challenges, primarily including:
Complex Geographic Environments: Pipelines often need to traverse oceans, deserts, mountains, and cold regions, each of which imposes different demands on pipeline materials. For instance, the salt mist in marine environments accelerates corrosion, while cold regions require pipelines to maintain good toughness at low temperatures.
Climate Variations: Climate differences across regions impact the lifespan and safety of the pipelines. Extreme conditions such as high temperatures, humidity, or freezing weather may damage pipeline structures, requiring materials that are highly adaptable.
Long-Distance Transportation: Transnational oil pipelines typically span thousands of kilometers, so they need to be highly pressure-resistant and stable to ensure safe transportation over long periods.
Suitability of API 5L Steel Pipes
API 5L steel pipes, with a series of excellent features, can meet the demands of transnational oil pipelines:
Corrosion Resistance: API 5L steel pipes use high-quality alloy compositions and anti-corrosion technologies, effectively resisting corrosion from marine environments, moisture, and salt mist, thus extending the service life of pipelines.
High Strength and Toughness: These steel pipes can withstand extreme temperatures and pressures, maintaining excellent performance and ensuring stability during long-distance transportation of oil and gas.
Compliance with International Standards: API 5L steel pipes meet the standards set by the American Petroleum Institute (API), ensuring their compatibility with regulations and requirements across different regions globally, making them suitable for international oil and gas transportation projects.
Good Weldability: API 5L steel pipes have good weldability, making them suitable for assembling and maintaining long-distance pipelines, ensuring reliable oil and gas transportation.
Environmental Adaptability of Transnational Oil Pipelines
Since transnational oil pipelines cross different climate zones and geographic environments, the environmental adaptability of API 5L steel pipes is crucial:
Tropical and Marine Environments: API 5L steel pipes’ corrosion resistance in tropical areas allows them to cope with high humidity, salt mist, and other environmental impacts, ensuring safe operation in these regions.
Cold Regions: API 5L steel pipes maintain good toughness in low-temperature environments, preventing cracking or brittleness in harsh cold climates, ensuring the pipeline’s stability and safety.
Mountainous and Desert Areas: API 5L steel pipes can withstand dust and extreme temperature differences, providing sufficient strength to prevent deformation or damage caused by changes in external environmental conditions.
Corrosion Resistance Technology of API 5L Steel Pipes
Corrosion is a major challenge in transnational oil pipelines due to their prolonged exposure to various environmental conditions, making them susceptible to natural elements, chemicals, and mechanical wear. The corrosion resistance technology of API 5L steel pipes significantly enhances the lifespan of pipelines, ensuring the safe and efficient transportation of oil and gas.
Impact of Corrosion Issues in Transnational Oil Pipelines
Transnational oil pipelines often span multiple countries and regions, crossing various geographic environments and climate conditions, making corrosion a more complex issue. Corrosion can lead to a reduction in the wall thickness of the pipes, structural weakening, and even leakage or rupture, posing serious risks to the environment, personnel safety, and oil and gas supply. The impact of corrosion on transnational oil pipelines can be seen in the following aspects:
Salt Mist Corrosion in Marine Environments: The salt mist in marine climates strongly accelerates the corrosion of steel pipes, particularly along coastal regions, where the salt and moisture hasten the oxidation process, causing surface damage.
Soil Corrosion: Moisture and chemical elements in the soil, such as sulfides and acids, can corrode underground pipelines, reducing their pressure resistance.
Temperature Variations and Moisture: In colder regions, temperature fluctuations can cause cracking or brittleness in steel pipes, while moisture in the air may lead to condensation on the surface of the pipes, further accelerating corrosion.
Corrosion Resistance Technology of API 5L Steel Pipes
To address the corrosion issues in transnational oil pipelines, API 5L steel pipes employ a series of advanced corrosion resistance technologies. These technologies effectively improve the durability of the pipes, ensuring stable operation in harsh environments.
External Coating Protection: API 5L steel pipes are often coated with multiple layers of anti-corrosion coatings such as epoxy coatings, polyethylene coatings, and polypropylene coatings. These coatings effectively isolate the pipe surface from moisture, air, and chemicals, preventing corrosion by keeping harmful agents away from the steel surface.
Internal Lining Coating: In certain cases, the interior of API 5L steel pipes is lined with corrosion-resistant coatings, such as epoxy resin or polyurethane coatings. This anti-corrosion technology mainly reduces internal corrosion during oil and gas transportation, extending the life of the pipeline.
Cathodic Protection: Cathodic protection technology involves installing sacrificial anodes on the exterior surface of the pipeline to prevent the steel pipe from losing electrons, thereby reducing the corrosion rate. This technology is especially useful for underground or underwater pipelines.
Alloying Technology: By adding alloy elements such as chromium, molybdenum, and nickel to the steel pipe, the corrosion resistance of the pipes is significantly enhanced. Alloyed steel pipes perform excellently in resisting various corrosive media, especially in acidic environments.
Surface Treatment of Steel Pipes: API 5L steel pipes can undergo mechanical or chemical treatments, such as phosphating or sandblasting, to increase the surface’s corrosion resistance and adhesion, reducing oxidation.
Case Studies
In real-world applications of transnational oil pipelines, the corrosion resistance technology of API 5L steel pipes has proven to be crucial.
Case 1: Oil Pipeline Crossing the Ocean
In a long-distance oil and gas transportation project crossing the ocean, API 5L steel pipes were coated with epoxy and polyethylene layers for corrosion protection. This project traversed multiple tropical sea areas, where the salt mist environment posed a serious corrosion threat. The coating became the key protective layer, significantly extending the pipeline’s lifespan and preventing damage caused by marine corrosion.
Case 2: Oil and Gas Transportation in Cold Regions
In an oil and gas transportation project located in a cold region, API 5L steel pipes were alloyed and equipped with cathodic protection. Due to the risk of cracking or brittleness in extreme cold, alloyed steel pipes provided better low-temperature toughness, while cathodic protection effectively prevented corrosion from soil and snow.
Selection of API 5L Steel Pipes and International Standards
In the oil and gas transportation industry, API 5L steel pipes are widely used globally due to their exceptional performance and compliance with international standards. The correct selection of suitable API 5L steel pipes is crucial to ensuring the safety, stability, and longevity of oil pipelines. This article explores the basis for selecting API 5L steel pipes and their relationship with international standards.
Basis for Selecting API 5L Steel Pipes
Selecting the appropriate API 5L steel pipe involves several factors, including the following:
Pipeline Usage and Pressure Rating: API 5L steel pipes come in various grades suitable for different pressure ratings in oil and gas transport. Depending on the design pressure of the pipeline, the corresponding API 5L grade such as X42, X46, X52, or X60 can be selected. Higher grades indicate stronger pipes, suitable for high-pressure and extreme conditions in oil and gas transportation.
Material and Alloy Composition: API 5L steel pipes are available in different material types, including carbon steel and alloy steel. The alloy composition enhances the pipe’s corrosion resistance, high-temperature endurance, and tensile strength. For transnational oil pipelines, selecting API 5L steel pipes with good corrosion resistance and high strength is critical for coping with environmental challenges in various regions.
Environmental Adaptability: API 5L steel pipes perform differently under various environmental conditions (such as marine, cold regions, etc.). For coastal areas or marine environments, pipes with strong corrosion resistance are essential, while in cold regions, the low-temperature toughness of the steel pipe is a key consideration.
Pipe Size and Specifications: API 5L steel pipes come in various sizes, including different outer diameters and wall thicknesses. The selection of pipe size directly affects the flow capacity, installation difficulty, and long-term maintenance costs of the pipeline. Choosing the correct size ensures stable oil and gas transportation without unnecessary resource waste.
API 5L Steel Pipes and International Standards
API 5L is a standard developed by the American Petroleum Institute (API), widely applied in the design and manufacturing of oil and gas pipelines. It provides clear technical specifications for pipe production, testing, and quality control to ensure pipeline products’ safety and applicability globally. The relationship between API 5L steel pipes and other international standards is as follows:
Compliance with International Transportation Requirements: API 5L steel pipes meet the global requirements for oil and gas pipelines, ensuring that the pipes meet strict specifications for quality, pressure resistance, and corrosion resistance in various countries and regions. As a result, API 5L steel pipes are extensively used in transnational oil and gas transportation projects.
Compatibility with ISO Standards: API 5L steel pipes are largely compatible with the International Organization for Standardization (ISO) standards in many respects. For example, API 5L X70 steel pipes are highly consistent with the relevant requirements in ISO 3183 standards regarding high temperature and corrosion resistance. Therefore, selecting API 5L steel pipes meets both domestic U.S. regulations and international standards in other countries.
Compliance with Pipeline Quality Control Standards: API 5L standards include stringent requirements for steel pipe materials, manufacturing processes, non-destructive testing, strength, and dimensions. This ensures that the pipes meet high-quality standards. API 5L-compliant pipes are widely recognized globally, which is particularly important for transnational oil and gas pipelines where compliance with international quality standards is vital.
Support for Pipeline Maintenance and Inspection: The API 5L standard not only ensures the quality of steel pipes during production but also provides detailed guidelines for pipeline maintenance, inspection, and repair. This is crucial for transnational oil pipelines, as ongoing maintenance and inspection are essential to ensuring the pipeline operates safely and effectively.
Quality Control and Testing of API 5L Steel Pipes
In the oil and gas transportation industry, API 5L steel pipes are widely used for their superior performance and strict manufacturing standards. To ensure that API 5L steel pipes meet design requirements and perform safely over extended periods, stringent quality control and testing procedures must be followed. These processes are critical for ensuring the safety, stability, and durability of pipelines. This article explores the quality control and testing methods for API 5L steel pipes.
Quality Control of API 5L Steel Pipes: Quality control for API 5L steel pipes involves monitoring the entire production process, from raw material selection to final product delivery, ensuring that each steel pipe meets the required standards. Key quality control measures include:
Raw Material Control: Quality control begins with the selection of raw materials. Steel manufacturers must use steel that complies with API 5L standards, ensuring that the chemical composition, mechanical properties, and other factors meet requirements. Materials are sourced from verified suppliers to prevent raw material issues that could impact the final quality of the pipes.
Monitoring During Production: During the production of steel pipes, the manufacturing process is continuously monitored to ensure the pipe’s forming, welding, heat treatment, and other processes meet the necessary standards. For example, during welding, it is critical to ensure the welds meet API 5L requirements to avoid defects such as cracks or porosity.
Dimensional and Visual Inspection: The pipe’s outer diameter, wall thickness, and length must be inspected to ensure they meet API 5L standards. These inspections help guarantee the pipe’s dimensional accuracy, avoiding defects such as scratches or dents on the surface, which could compromise the pipe’s performance.
Mechanical Property Testing: The mechanical properties of API 5L steel pipes, including tensile strength, yield strength, elongation, and impact toughness, must be rigorously tested. Common tests include tensile tests, yield strength tests, elongation tests, and impact tests, all of which ensure the pipe can withstand external pressure and environmental changes.
Testing Methods for API 5L Steel Pipes
Several testing methods are employed to ensure API 5L steel pipes meet quality standards. Common testing methods include:
Non-Destructive Testing (NDT)
Non-destructive testing is a critical part of ensuring API 5L steel pipes meet quality requirements. Common NDT methods include:
Ultrasonic Testing (UT): Used to detect internal defects, such as cracks or voids, within the steel pipe. Ultrasonic waves are reflected off defects, allowing for detection of internal and external pipe quality issues.
Radiographic Testing (RT): Using X-rays or gamma rays, this method inspects welded areas and surfaces for defects such as cracks, pores, or inclusions.
Magnetic Particle Testing (MT): This method detects surface cracks on the pipe by applying a magnetic field and sprinkling magnetic particles over the surface, revealing any surface defects.
Dye Penetrant Testing (PT): Used to detect small surface cracks and holes, dye penetrants seep into defects and highlight the flaw for easier inspection.
Chemical Composition Analysis
The chemical composition of API 5L steel pipes, including elements such as carbon, silicon, manganese, sulfur, and phosphorus, must comply with the standard. Chemical analysis, such as spectroscopy, is used to confirm the material’s compliance with the API 5L specifications.
Pressure Testing
Pressure testing is conducted to assess the pipe’s ability to withstand pressure. Common methods include hydrostatic tests (using water) and pneumatic tests (using air or gas). These tests apply pressure to the pipe to check for leaks or failures under specific pressure conditions.
Surface Quality Inspection: The surface quality of the pipe is a key indicator of its overall quality. Surface inspections check for issues like cracks, scratches, dents, and oxidation that could impact the pipe’s sealing ability and corrosion resistance.
Dimensional Inspection: The dimensions of the steel pipe, such as outer diameter, wall thickness, and length, must meet the specified API 5L standards. Dimensional inspections ensure that the pipe will fit properly during installation and meet the required operational standards.
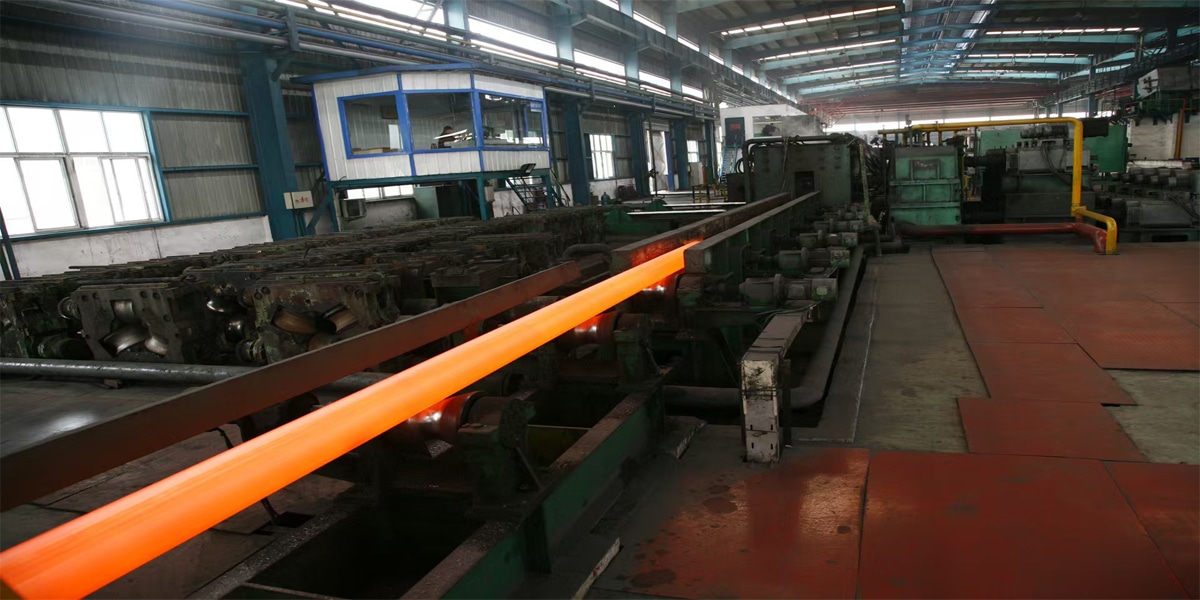
Future Trends of API 5L Steel Pipes in Transnational Oil Pipelines
As global energy demands continue to rise and the need for oil and gas transportation increases, the application of API 5L steel pipes in transnational oil pipelines will continue to evolve, facing new challenges and opportunities. The future trends will mainly focus on technological innovations, environmental adaptability, pipeline maintenance, and international standardization. Below are the future trends of API 5L steel pipes in transnational oil pipelines.
1. Higher Pipe Grades and Strength Requirements
With increasing transportation pressures and extended transportation distances, the required pipe grades and strength for API 5L steel pipes will continue to rise. Higher steel pipe strength ensures that pipelines can withstand greater pressure, especially in deep-sea and extreme geological environments. API 5L X70, X80, and X100, higher-grade steel pipes, will gradually become the mainstream in market demand to meet the needs of high-pressure and long-distance oil pipelines.
2. Optimized Corrosion Protection Technologies
In transnational oil pipelines, environmental factors significantly influence the corrosion of steel pipes. In the future, corrosion protection technologies for API 5L steel pipes will become more advanced, including the use of new alloy materials, more efficient coating technologies, and double-layer protection with internal and external coatings. These technologies will effectively improve the corrosion resistance and service life of steel pipes, especially in coastal, cold, and humid environments.
3. Enhanced Environmental Adaptability
As the impact of climate change becomes increasingly evident, future API 5L steel pipes will need to exhibit higher environmental adaptability. For example, in extremely low-temperature regions, the toughness and crack resistance of steel pipes will be key design factors. Additionally, under high-temperature, high-pressure, and seabed conditions, the material selection and manufacturing processes of steel pipes will be stricter to ensure pipeline safety and stability.
4. Intelligent and Automated Inspection Technologies
With the continuous advancement of technology, intelligent and automated technologies will be widely applied in the inspection and maintenance of API 5L steel pipes. For instance, intelligent sensors and IoT technologies will be used for real-time monitoring of oil and gas pipelines, enabling early detection of potential failures or corrosion issues. Automated inspection equipment will enhance testing efficiency and precision, reducing human error and further ensuring the safety of transnational oil pipelines.
5. Sustainability and Green Energy Development
As global attention shifts towards sustainable development and green energy, the production of API 5L steel pipes will focus more on environmental protection and resource conservation. Steel pipe manufacturers will adopt more environmentally friendly production processes to reduce carbon emissions and optimize resource utilization efficiency. At the same time, API 5L steel pipes will be widely used in the transportation of green energy pipelines, such as natural gas, hydrogen, and renewable energy, contributing to the global energy transition.
In conclusion, API 5L steel pipes will continue to play a crucial role in transnational oil pipelines, meeting the growing demands of the oil and gas industry. With improvements in strength, corrosion resistance, and environmental adaptability, these pipes will continue to support the safe and efficient transportation of oil. The application of smart technologies and adherence to international standards will further enhance their reliability, ensuring their significant role in future global energy transmission. If you have any further questions, feel free to contact us. We are always here to assist you!