In today’s global infrastructure and energy transportation sectors, the demand for steel pipes continues to rise, especially in critical industries such as oil, gas, and water treatment. Among various steel pipe standards, ASTM A671 steel pipes stand out for their exceptional performance and reliability, making them a key choice in the industry. Whether it’s their corrosion resistance in extreme temperatures or strength in high-pressure environments, ASTM A671 steel pipes are engineered to meet stringent requirements. However, this reliability and quality are only achieved through precise manufacturing processes and rigorous quality control! In this article, we will explore the manufacturing process of ASTM A671 steel pipes, from raw material selection to the final inspection of the finished product. We will also take a closer look at how the demand for high-quality steel pipes is evolving in the modern market and examine how scientific quality control methods ensure that each pipe meets international standards, providing a solid foundation for energy transportation and water treatment applications!
Overview of ASTM A671 Steel Pipes
Standard Introduction: ASTM A671 is a standard issued by the American Society for Testing and Materials (ASTM) that specifically governs the manufacturing requirements of low-alloy steel welded pipes used in industries such as oil, gas, and water treatment. This standard is applicable to large-diameter steel pipes primarily used in high-pressure, high-temperature, or harsh environmental pipeline systems. ASTM A671 steel pipes are manufactured with strict requirements to ensure superior mechanical properties, corrosion resistance, and weldability, making them widely used in oil and gas transportation, cross-border energy pipelines, and water treatment projects.
Scope of Application:
The ASTM A671 standard covers the technical requirements for welded steel pipes, including the chemical composition of raw materials, manufacturing processes, mechanical properties, dimensional accuracy, and surface treatments. It is primarily used in high-pressure, low-temperature, and other complex environments, particularly for the following applications:
Oil and Gas Transmission: Used in pipelines for oilfield and natural gas extraction.
Cross-border Transportation: Suitable for long-distance international energy pipeline transportation.
Water Treatment Systems: Widely used in water treatment pipelines, especially in environments requiring high corrosion resistance.
Energy Pipelines: Applied in the power and nuclear industries for related pipeline systems.
Key Performance Indicators:
Mechanical Properties: ASTM A671 steel pipes must meet stringent mechanical property requirements, including tensile strength, yield strength, and elongation. Typically, the tensile strength should not be less than 485 MPa, and the yield strength should not be less than 275 MPa.
Corrosion Resistance: ASTM A671 steel pipes offer excellent corrosion resistance, especially in harsh environments like marine and acidic conditions. This makes them ideal for use in environments that demand high resistance to corrosion.
Weldability: Given their use in long-distance and high-pressure applications, the weldability of ASTM A671 steel pipes is crucial. The standard requires that the pipes be suitable for welding using various methods, with the welded joints needing to meet strict quality standards.
Dimensional Tolerances and Shape: The external diameter, wall thickness, and length of ASTM A671 steel pipes must meet specific tolerance requirements to ensure compatibility with the required strength and adaptability. The surface of the pipe must be smooth and free from defects to ensure tight sealing and pressure resistance during installation and operation.
Surface Treatment: The surface of ASTM A671 steel pipes must be free from visible cracks, porosity, inclusions, and other defects. They also require appropriate surface treatments, such as corrosion-resistant coatings, to extend their lifespan in harsh environments.
Manufacturing Process of ASTM A671 Steel Pipes
The manufacturing process of ASTM A671 steel pipes encompasses several stages, from raw material selection and pipe formation to welding, heat treatment, and final inspection. Each stage is critical to ensuring the pipes’ reliability in high-temperature, high-pressure, and corrosive environments. Below is a detailed description of the main steps involved in the manufacturing process:
1. Raw Material Selection
Steel Source: The raw materials used for ASTM A671 steel pipes are primarily low-alloy steel plates or coils. The chemical composition of these materials must comply with the requirements specified in ASTM A671, including elements like carbon, manganese, silicon, phosphorus, and sulfur.
Quality Inspection: The steel materials undergo rigorous chemical and mechanical property tests to ensure they meet the necessary standards for strength, weldability, and corrosion resistance.
2. Pipe Formation
Hot Rolling or Cold Rolling: Depending on the pipe’s size and specifications, the steel plates or coils are formed into a pipe shape through hot or cold rolling processes. This step shapes the steel into the preliminary pipe form and ensures that it meets the required dimensions.
Heat Expansion: For larger diameter pipes, heat expansion may be used to achieve the required internal and external dimensions as well as wall thickness.
3. Welding
Submerged Arc Welding (SAW): ASTM A671 steel pipes are primarily manufactured using the submerged arc welding process, which ensures high-strength and high-quality welded seams. This process involves welding the steel pipe’s longitudinal seam, ensuring strong fusion and excellent corrosion resistance of the weld.
Welding Materials: The welding materials used must be compatible with the base steel to ensure a strong, durable bond between the welded parts of the pipe.
4. Heat Treatment
Annealing and Normalizing: After welding, the steel pipe typically undergoes annealing or normalizing treatment to relieve welding stresses and improve mechanical properties. This process also ensures that the steel pipe’s microstructure is uniform, enhancing its toughness and resistance to cracking.
Water or Oil Cooling: In some cases, water or oil cooling is used to control the cooling rate, ensuring precise dimensions and a uniform internal structure.
5. Dimension and Wall Thickness Adjustment
After heat treatment, the pipe is further adjusted for its diameter, wall thickness, and length to ensure it conforms to the ASTM A671 standard. Methods such as cold drawing or cold rolling may be employed for precise dimensional control.
6. Surface Treatment
Pickling and Sandblasting: To remove oxidation scales and impurities from the pipe’s surface, the steel pipes are usually subjected to acid pickling.
Afterward, processes like sandblasting are used to smooth and clean the surface, ensuring that the pipes are free of defects and are ready for further use.
Coating: In certain applications, the surface of the steel pipe may be coated to enhance its corrosion resistance.
7. Quality Inspection and Testing
Visual Inspection: The pipe’s surface is checked for any defects such as cracks, porosity, or inclusions to ensure a high-quality finish.
Dimensional Measurement: The pipe’s external diameter, wall thickness, and length are measured using precision instruments to ensure compliance with ASTM A671 dimensional requirements.
Mechanical Property Testing: Tests for tensile strength, yield strength, and elongation are conducted to ensure that the pipe has sufficient strength and ductility for its intended applications.
Non-destructive Testing: Methods such as ultrasonic testing and X-ray inspection are used to check the weld seams and the pipe’s interior for any potential defects that could compromise its integrity.
8. Packaging and Delivery
After passing all tests and quality checks, the pipes are packaged according to customer specifications. Packaging typically involves protective materials that guard against moisture and rust, ensuring the pipes remain in good condition during transportation.
The steel pipes are accompanied by quality certificates and inspection reports, allowing customers to trace the manufacturing process and performance of each pipe.
Quality Control Measures for ASTM A671 Steel Pipes
1. Process Quality Monitoring:
Quality control for ASTM A671 steel pipes encompasses every stage of production, from raw material procurement to the final product. Process quality monitoring ensures high standards are maintained through the following measures:
Raw Material Control: The quality of raw materials forms the foundation of steel pipe performance. Materials must meet the chemical composition and physical properties specified by the ASTM A671 standard. Manufacturers are required to ensure that steel procured from suppliers meets these standards and undergoes necessary in-house testing.
Production Process Control: Strict control is maintained at every stage of pipe production, including heat treatment, welding, forming, and cooling. The heat treatment process must ensure the steel pipes’ durability and strength in both high and low-temperature environments, while welding procedures are closely monitored to guarantee the structural stability and pressure resistance of the pipes.
Dimensional and Appearance Control: During production, the external diameter, wall thickness, length, and other dimensions of the steel pipes are carefully monitored to ensure they meet the tolerance requirements specified by ASTM A671. Surface treatment is also an important part of quality control, ensuring that pipes are free from visible cracks, porosity, and other defects.
2. Testing and Certification Standards:
To ensure that ASTM A671 steel pipes meet international standards, manufacturers must adhere to a series of testing and certification procedures:
Mechanical Property Testing: Mechanical properties such as tensile strength, yield strength, and elongation must be verified through tensile tests and hardness tests. Random sampling from each production batch is conducted to ensure compliance with the standard requirements.
Chemical Composition Analysis: The chemical composition of the steel pipes must meet the requirements outlined in the ASTM A671 standard.
Spectroscopic analysis and other methods are used to ensure that the alloy elements are properly included and that the raw materials are compliant.
Non-Destructive Testing (NDT): Steel pipes undergo non-destructive testing methods such as ultrasonic testing and X-ray inspection to detect any cracks or defects in the welds and the internal structure of the pipes. These tests effectively prevent hidden quality issues from going unnoticed.
Surface Inspection and Coating Tests: Surface inspection ensures that the pipes are free from visible defects such as cracks, scratches, and bubbles. In addition, the thickness and adhesion of corrosion-resistant coatings are tested to ensure the pipes can withstand harsh environments.
International Certifications and Compliance Testing: Manufacturers often seek international certifications such as ISO 9001 (Quality Management System) and API certifications to guarantee that their products meet global standards. Third-party inspection agencies are also involved to verify compliance with all requirements outlined in ASTM A671.
3. Post-Maintenance and Feedback Mechanisms:
Post-maintenance and feedback mechanisms are essential for ensuring the long-term reliability of ASTM A671 steel pipes. The following measures track and address the performance of the pipes throughout their service life:
Usage Monitoring: Regular inspections and maintenance are performed on installed pipelines, especially those exposed to high pressures, extreme temperatures, and corrosive environments. Periodic pressure testing and corrosion monitoring help detect potential safety hazards and prevent failures due to quality issues.
Customer Feedback Mechanism: Manufacturers should establish a robust feedback mechanism to collect information from customers regarding any issues or suggestions during usage. By analyzing real-world data, manufacturers can assess the long-term performance of their pipes and adjust production processes and quality control measures accordingly.
Regular Maintenance and Service: Post-installation maintenance typically involves routine cleaning, anti-corrosion treatments, and replacing damaged components, especially in corrosive environments. Manufacturers can provide ongoing technical support and maintenance services to extend the lifespan of the pipes.
Quality Traceability System: A comprehensive quality traceability system allows manufacturers to track each pipe’s production, testing, and usage history. This system ensures that any quality issues can be quickly identified and resolved.
The Role of Manufacturing and Quality Control in High-Performance Applications:
Ensuring Structural Integrity and Reliability: The precise manufacturing process and rigorous quality control ensure that ASTM A671 steel pipes maintain structural integrity under high-pressure and high-temperature conditions. This is particularly important in sectors like oil and gas, where pipeline failures can result in catastrophic consequences.
Optimizing Performance in Harsh Conditions: ASTM A671 steel pipes are designed to perform optimally under extreme conditions, including high pressure, temperature, and corrosive environments. Through controlled welding, heat treatment, and surface treatment, the pipes are made to have the necessary strength, flexibility, and durability to meet the demands of these challenging environments.
Enhancing Lifespan and Reducing Maintenance Costs: The robust manufacturing process and stringent quality control ensure that ASTM A671 steel pipes have a long service life, even in demanding environments. This reduces the need for frequent maintenance or replacement, lowering long-term operational costs and increasing system reliability.
Compliance with Industry Standards: High-performance applications require materials that meet strict industry standards. The manufacturing process of ASTM A671 steel pipes guarantees compliance with international standards such as API, ISO, and ASME, ensuring that the pipes meet global quality and safety benchmarks. This is essential for projects in critical sectors like oil and gas, where regulatory compliance is a non-negotiable requirement.
Case Study Analysis of ASTM A671 Steel Pipe Applications
ASTM A671 steel pipes, known for their exceptional performance, are widely used in industries such as oil, gas, power generation, and water treatment. Below are several case studies that demonstrate the application value of ASTM A671 steel pipes in various environments and conditions.
1. Oil and Gas Pipeline Project
In the transportation of oil and gas, pipelines must withstand high pressure, extreme temperatures, and corrosive environments. An oil company used ASTM A671 steel pipes in the construction of a pipeline for its offshore oil field project. The specific challenges of the project included:
High-Pressure Environment:
The pipeline was designed to operate at a pressure of up to 1200 psi, and the steel pipes needed to have sufficient strength to avoid cracking or bursting due to internal pressure. ASTM A671 steel pipes demonstrated excellent reliability under high pressure, ensuring the safe transportation of oil.
Corrosion Resistance:
Due to the corrosive saltwater environment, ASTM A671 steel pipes were coated with specialized surface treatments such as shot blasting and anti-corrosion coatings, significantly improving their resistance to corrosion. Salt spray testing and other inspections confirmed the pipes’ superior corrosion resistance, effectively extending their service life.
2. Water Treatment Pipeline Project
In the water treatment industry, pipelines are frequently exposed to chemicals and acidic water environments. A water treatment plant used ASTM A671 steel pipes in its wastewater transportation system. The challenges and solutions for this project included:
Chemical Corrosive Environment:
Wastewater contains numerous chemicals that are highly corrosive. ASTM A671 steel pipes were treated with advanced surface coatings, such as internal and external coatings, to protect against the corrosive environment. These treatments greatly enhanced the pipes’ corrosion resistance, ensuring long-term reliable operation.
Pressure Resistance:
The wastewater treatment system required the pipes to withstand relatively high internal pressures. ASTM A671 steel pipes, through precise welding techniques and strength-optimized designs, demonstrated high pressure resistance, preventing rupture or leakage under demanding operational conditions.
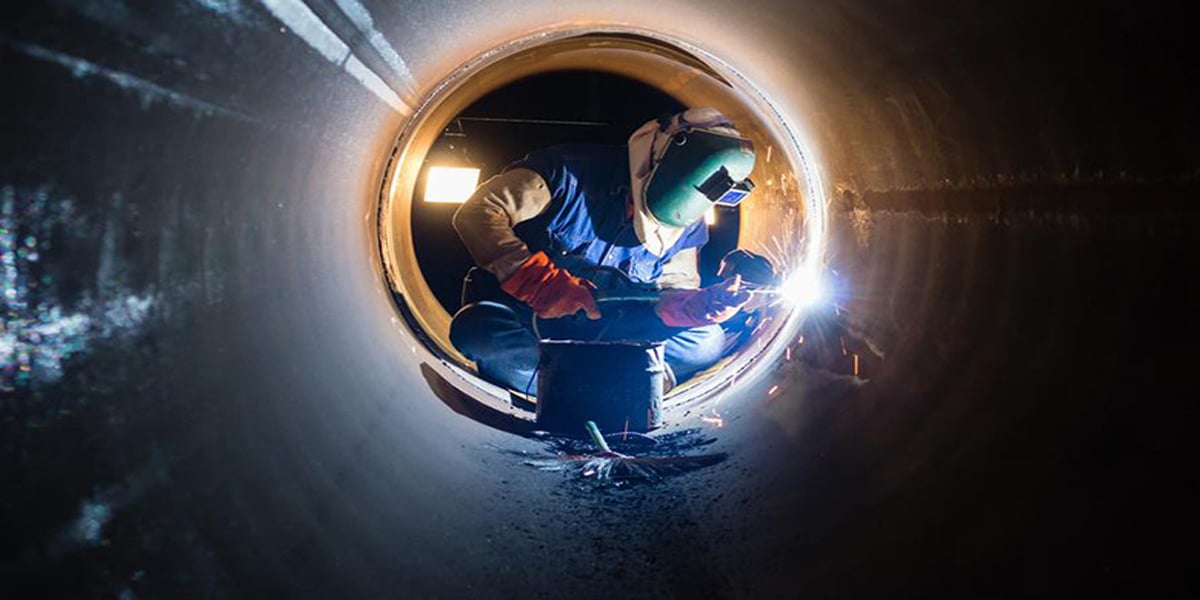
Future Trends and Continuous Improvement of ASTM A671 Steel Pipes
As industries continue to evolve and demand higher performance, the future of ASTM A671 steel pipes lies in addressing the emerging challenges posed by environmental sustainability, technological advancements, and increasingly stringent regulatory requirements. To maintain its competitive edge and meet these evolving needs, continuous improvement and innovation in manufacturing and quality control are essential. Below are key future trends and areas for continuous improvement in ASTM A671 steel pipes:
1. Enhanced Corrosion Resistance and Sustainability
Increased Focus on Environmental Sustainability:
With growing concerns over environmental impacts, the future of ASTM A671 steel pipes will likely involve improvements in their corrosion resistance to ensure longer service life, especially in harsh environments such as offshore oil rigs, wastewater treatment plants, and chemical processing industries.
Innovations in eco-friendly anti-corrosion coatings, such as bio-based or low-impact coatings, are expected to reduce the environmental footprint of steel pipes while improving their durability.
Use of Advanced Alloys and Coatings:
New alloy compositions and advanced coatings that provide superior resistance to corrosion, especially in aggressive chemical and marine environments, are likely to be developed. For instance, the introduction of duplex stainless steel or titanium-based alloys in the manufacturing of ASTM A671 pipes could improve their resistance to chloride-induced corrosion and extend their lifespan in extreme conditions.
2. Smart Monitoring and IoT Integration
Incorporating Smart Technology:
The integration of smart monitoring technologies, including sensors embedded in the steel pipes, will become more common. These sensors can monitor the structural integrity of pipes in real time, detecting signs of corrosion, stress, or potential failure before they become critical issues. This will improve the predictive maintenance of pipeline systems, reducing the risk of unplanned downtime and increasing the reliability of pipeline infrastructure.
Internet of Things (IoT) in Pipeline Monitoring:
The incorporation of IoT technologies in ASTM A671 steel pipes will enable continuous data collection and real-time reporting on the condition of the pipeline. This will enable operators to better understand pipe performance, optimize maintenance schedules, and improve overall pipeline safety, leading to reduced costs and enhanced operational efficiency.
3. Automation and Robotics in Manufacturing
Automation in Production Lines:
The adoption of automation and robotics in the manufacturing of ASTM A671 steel pipes will significantly enhance production efficiency, reduce human error, and ensure consistent quality. Automated welding, inspection, and testing processes will become more widespread, ensuring the pipes meet the highest standards of precision and quality control.
Advanced Welding Techniques:
Next-generation welding technologies, such as laser welding or friction stir welding, will continue to improve the strength and integrity of weld seams, particularly in thicker pipes used for high-pressure applications. These methods offer greater precision and reliability compared to traditional welding techniques, ensuring better performance in demanding environments.
4. Enhanced Quality Control and Testing Standards
Automated Inspection Systems:
As part of ongoing quality improvement efforts, automated and advanced non-destructive testing (NDT) systems will become more prevalent. Technologies such as ultrasonic testing, X-ray inspection, and 3D imaging will become more sophisticated, enabling manufacturers to detect even the smallest defects and ensure pipe integrity throughout the production process.
AI and Machine Learning in Quality Control:
The integration of artificial intelligence (AI) and machine learning into the quality control process will allow manufacturers to better predict defects based on historical data and performance analytics. AI can also optimize manufacturing processes by identifying inefficiencies and suggesting improvements, ensuring the production of higher-quality pipes at a reduced cost.
As the demand for high-performance pipes continues to rise, ASTM A671 steel pipes will remain an essential component across various industries. With their excellent corrosion resistance, superior mechanical properties, and broad range of applications, they are the ideal choice for projects in the oil, gas, water treatment, and other critical sectors. Looking ahead, advancements in technology and growing sustainability requirements will drive further innovations in the manufacturing processes and quality control of ASTM A671 pipes to meet the evolving global market demands! In this context, LONGMA offers a wide range of ASTM A671 pipe products in various sizes, meeting the pipeline needs of water, oil, gas, and other industry applications. Our company manufactures and stocks multiple grades and classes of ASTM A671 EFW pipes, ensuring that each pipe maintains exceptional quality and reliability.
Whether used for structural purposes or fluid, gas, and oil transportation, our ASTM A671 carbon steel pipes provide optimal support for your projects. As your trusted manufacturer, LONGMA is committed to supplying high-quality ASTM A671 CS welded pipes and electric fusion welded pipes, supporting the infrastructure development of various industries. Choose LONGMA for strong quality assurance and technical support for your projects!